Thermal vs Magnetic/Hydraulic Circuit Breakers
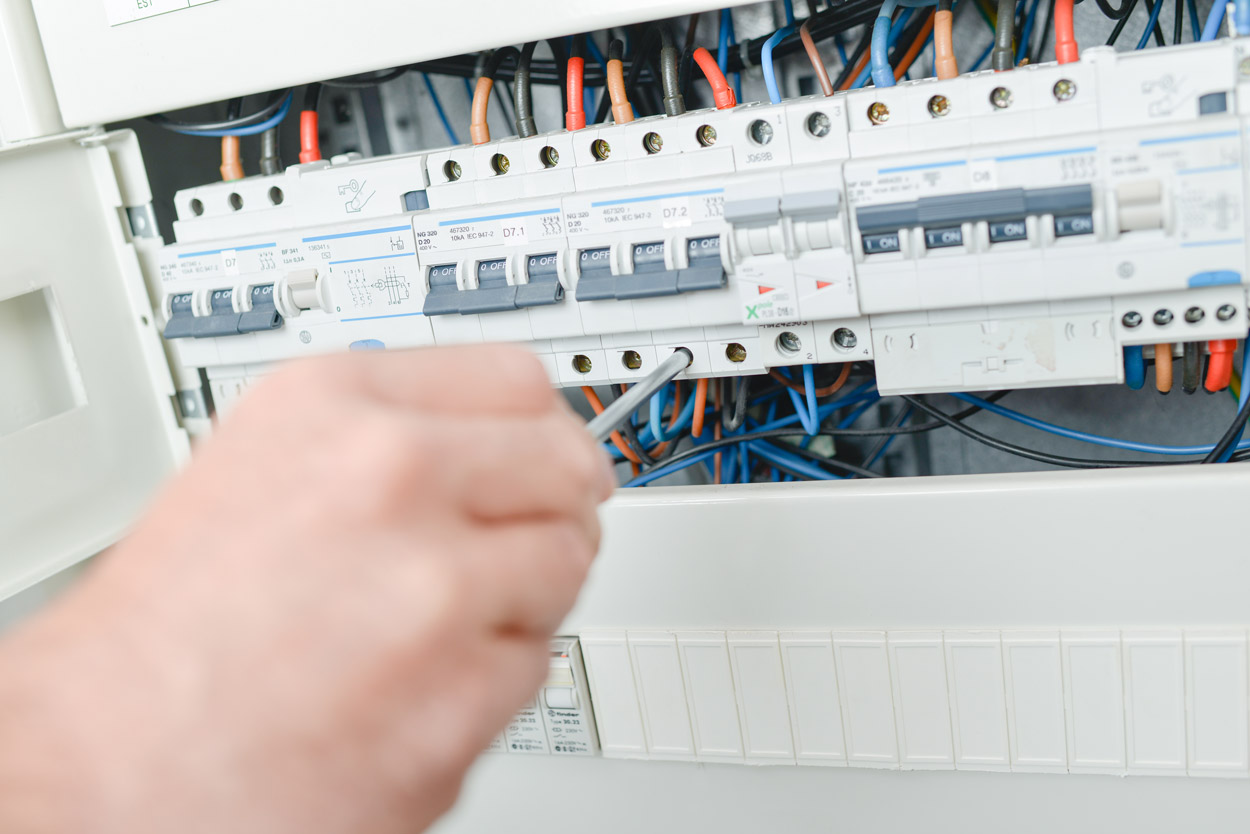
Since there a plethora of different kinds of circuit breakers available now, including some still on the drawing board stage harnessing emerging technologies, we shall concentrate on the two most common types – the thermal and the magnetic/ hydraulic circuit breakers.
So, at a very basic level, what is a circuit breaker?
It is nothing but a mechanical protection device against overcurrent or inrush currents, protecting the rest of the system from the electrical surge (oh yes, you have heard about digital circuit breakers, but we are sticking to the basics here!). They are meant to open a circuit, what we generally call ‘tripping’, as they sense excess current flowing through.
Now how this mechanism is achieved is what brings us to the two main types of circuit breakers we are here to discuss – thermal and magnetic/ hydraulic.
A thermal circuit breaker is nothing but a bimetallic strip which uses the thermoelectric principle of heat generated while current passes through metals, or, for that matter, any conductors. While the generated heat reaches a certain value, the thermally sensitive bimetallic strip bends, tripping an actuator that breaks the circuit.
The magnetic/ hydraulic circuit breaker, on the other hand, uses the principle of magnetic forces induced due to the flow of current. It basically consists of as electromagnetic coil or solenoid, a hydraulic fluid-filled tube containing an iron core and the usual actuator. As a definite amount of electric current passes through the electromagnetic coil, the induced magnetism moves the iron core to trip the actuator and break the circuit. The hydraulic fluid, depending on its viscosity, determines the ‘time-delay’ –the time the iron core needs to push through the fluid to reach and trip the actuator.
Now, this is the interesting part. If there was no hydraulic component, the magnetic circuit breaker, while reaching the threshold current, would have acted instantaneously. Sounds cool, right? A surge comes in, the circuit instantaneously trips. But remember, the circuit breakers are used in conditions where appliances like motors, HID bulbs etc. are plugged in. These generally draw momentarily a surge of current, much more than the rated value, while they start. If the hydraulic component was not there, all these would never start, if the circuit breaker were calibrated at the rated value, due to the near-instantaneous tripping (that’s the ‘nuisance tripping’ folks often complain about!). However, depending on the specific situation and the make of the overall circuit, the amount and viscosity of the fluid can be calibrated to adjust the time delay. Look for the manufacturer’s specification for details.
The thermal circuit breaker, on the other hand, works solely based on the temperature gradient. It has an inherent time-delay. Yes, guessed it right – the bimetallic strip, however thermally sensitive, takes a bit of time to ‘heat up’ before breaking the circuit. While it allows for the inrush current for motor starting etc. as mentioned above, check the specific need to the overall circuitry. Does it need instantaneous tripping, for whatever reasons? Then rethink the choice of a thermal circuit breaker. A magnetic/ hydraulic circuit breaker, suitably calibrated, could be better choice hands down.
Now, what if the circuit breaker is not in a controlled environment, say, like in the airconditioned confines of a data center? Is it out in the open? Is the ambient temperature albeit too high or too low? Since the device relies solely on temperature triggered tripping, it is prone to get affected by temperature fluctuations. It may trip at a lower current at a higher ambient temperature and may not trip as needed at a higher current while the ambient temperature is low. Simply because, the total heat triggering the actuator by bending of the bimetallic strip would be affected by the sum of the heat generated, one by the current flowing and the other, the ambient temperature (which, as rightly guessed, would negatively affect the heating if it is kind of low).
And be sure to factor in the ‘cool-down’ period of thermal circuit breakers before they can be reset while making your choice. Depending on the make of the thermal circuit breaker, the reset time may take anything from a couple of minutes to about half an hour ( e.g. 3 mins for 100AF, 20 mins for 800AF). This is a big drawback for application in situations where near-instantaneous resetting is expected. The magnetic/ hydraulic one obviously does not have this inherent handicap as they do not rely on the heating effect of the current and neither the solenoid nor the hydraulic fluid needs any cooling off period.
Also, in the case of the thermal type of circuit breakers, to compensate for the ambient temperature, you may like to check the manufacturer’s guidelines on “Rated Current Compensation Curve”. Normal recommendation is to keep the load current such that it is lower than 80% of the rated current. For magnetic/ hydraulic circuit breakers the rated current can practically be selected without factoring in any change in the ambient temperature. Typically all magnetic/ hydraulic circuit breakers come with a choice of three time delay curves – slow, medium and long. This add to the flexibility of the designer.
The magnetic/ hydraulic circuit breakers also have the big advantage of the ease of manufacturing for different rated currents. Based on the principle of electromotive force equal to the product of the current and the number of turns of the coil, by changing the number of turns of the coil in the solenoid, any rated current may accurately be obtained by calculating and varying the number of turns in the coil. Unfortunately for thermal types, such flexibility is difficult, if not practically infeasible, as it would involve precise free-cutting of the bimetal strips for any instance of change (they are normally available for ‘standard’ values like 10A or so).
Well, everything said and done, it’s still not doomsday for thermal circuit breakers though. They are still ahead of thermal/ hydraulic ones in one area – they pinch our pockets less! Since they are cost effective, if you are planning to use a circuit breaker in temperature controlled environment where the added appliances and other circuit elements can make do with a reset time delay ( and mind you, no people complaining or the phone lines getting choked reporting ‘outages’!), you can still make do with the good old thermal circuit breakers!
Tip: It is generally required for magnetic/ hydraulic circuit breakers that they be mounted vertically, else, the effect of gravity has a chance to affect the time taken for the iron core to move through the hydraulic fluid to trip the actuator and break the circuit. However small the effect might be, depending on the installation and overall circuitry, it is one of the finer points most often missed by the most experienced of engineers too! Thankfully, for thermal circuit breakers, they are not restrained on this front!
Tip: To quickly know the threshold activating the magnetic tripping, check the label on the circuit breaker. It indicates the threshold of activating the tripping mechanism in a magnetic / hydraulic circuit breaker. As a guideline, B, C & D labelled circuit breakers trip at 3 to 5 times, 5 to 10 times and 10-20 times the rated current respectively.